Installation
Before beginning the installation, suitability of the existing structure must be checked due to the steel and architectural project. The contractor firm must be informed if the purlines deviate from their lines, are dirty and if there is no sufficient surface width for installation. Extra flange parts may need to be mounted.
Gloves should be worn for protection against cut and bruises during installation. To not to harm panel surface, installation staff should always wear rubber shoes. While the montage of roof panels, to walk by stepping of roof ribs is appropriate.
Gloves should be worn for protection against cut and bruises during installation. To not to harm panel surface, installation staff should always wear rubber shoes. While the montage of roof panels, to walk by stepping of roof ribs is appropriate.
While sandwich panels are raised to the point where they will be applied, they shouldbe moved by being compressed with a vacuum suction or U shaped hook. If lifted with a hook, the hole provided on the panel edges must be closed with the accessories.
The panel can be cut due to the project before it is lifted to the point where it will be applied. Since this process will weaken the cross section of the sandwich panels, the region cut before lifting should be strengthened with angle braces.
A suitable saw or decoupage must be used for cutting the panels. The surface of the saw must be cold to prevent damage to the panel surface.
Painted surfaces must be protected while welding or cutting. The metal wastes generated during welding or cutting, must be swept up with a brush immediately. Otherwise, they can cause corrosion in a few months.
If there is protective foil on panels, it should be removed from roof panels surface before screwing and from wall panels immediately after montage.
The accessories that should remain under the roof and wall panels (bottom ridge profile, bottom eave profile, valley, gutter, drip flashing, internal corner profiles, etc,) must be installed before the panels. Direction of the prevailing wind in the region should be determined and for the roof panels the installation direction should be against the wind direction and for wall panels due to joining detail installation direction should be same with the wind direction.
Thermal bridges and corrosion risk should be avoided by applying a butyl tape or a suitable insulation material on the surfaces where the steel purline and sandwich panel contact each other. It must be covered with the accessories immediately after the panel installation is completed. Especially, the fillings of the rockwool and glasswool insulated panels must be protected against getting wet and moisture. Otherwise, the product will get wet by sucking up water inside and if it cannot be dried, the insulation material will decay and deteriorate in time.
During installation, all joint details should be sealed so as not to allow thermal bridge, air and water flow. Especially in the cold room panel applications, silicone joints must be sealed by mastic or silicone.
During the installation of the Metapanel products, suitable fasteners for the product and carrier system must be chosen. EPDM self drilling or swrews with high corrosion resistant and tensile strength should be used by taking into account the thickness of the panels, carrier system, wind and load conditions. Amount of screws vary according to the product type, ribbed distances and design details. Saddle should be used between the screws and panels in rockwool insulated panels montage because of rockwool panels fiberous and flexible character.
The screws should not be hammered during panel installation (except concrete screws) and with a proper torque setting they must not be used too tight or loose. Internal metal surface of the panel should join to the carrier system exactly, but it must be screwed without pressing or deteriorating the form of the external face of the panel.
If longitudinally overlapping is needed in the Sandwich Panel installation, the lap distance must be between min. 200-250 mm. In side laps, firstly the bottom panel and then the top panel is installed. The overlapping surfaces insulation must be done with butyl tape or silicone after the surface of laps cleaned and dried. Both panels should be fixed to the construction and at this point, opposite double spans must be mounted or the span surface must be extended so that both panels can be fixed. The joint detail must be supported with a pop rivet or puller screw.
After the roof and walls are covered, installation of accessories left above such as eaves, gables and corners must be completed. Accessories must be installed with 150 mm laps and insulation must be applied. The accessories which may be affected by the wind or which act as a carrier must not be used below 0.70 mm thick and they must be fixed from every purline point. In rockwool insulated panels, the insulation material must be closed with accessories at the eave and skirting point to prevent getting water inside.
The perimeter of the skylight or ventilations in roof should be covered with sheet metal or accessories. In order to extend the life of Sandwich Panels, panels and accessories should be checked at least once a year. Screws, scratches and tears of the panel surfaces should be controlled, the areas receiving water and the damaged accessories by the effects of weather conditions must be identified and if any, these must be restored.
The dirt accumulated on the painted metal surface during or after installation, can be cleaned using water and conventional cleaning equipments. Panel surfaces should be washed once a year with unpressurized water, if there are stains or dirt, it must be cleaned with a soft sponge and water-based detergent. Solvent and chemical solvents must not be used for cleaning not to harm paint. If there are scratches on the panel surface, they must be modified with air-drying touch-up paint or with a painter brush.
If Transportation, Unloading, Storage and Installation are performed in a manner other than the points mentioned herein, the product become out of warranty.
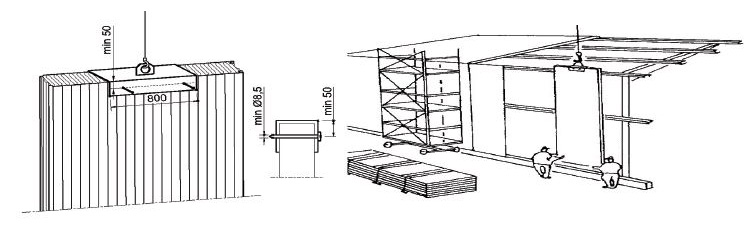